Aircraft types that I have flown
I was asked to fill out a form showing the aircraft that I have flown and it turned out to be a longer list than expected…
- 8KAB (Decathlon)
- AA5 (Grumman Tiger)
- AC95 (Twin Commander 1000 turboprop)
- B200 (King Air 200 turboprop)
- B206
- B505 (new Jet Ranger)
- BE36
- BE55
- BE58
- BE103 (Beriev twin-engine seaplane!)
- C172
- C182
- C210 (in southern Africa)
- C310 (crazy noisy!)
- C510 (Cessna Mustang jet)
- CJ3
- CL65 (Canadair Regional Jet)
- COL4 (Columbia 400/Cessna 400)
- DA20 (Diamond Katana)
- DA40 (Diamond Star)
- EMB-500 (Phenom 100 jet)
- Evolution (experimental turboprop)
- Gamebird GB1
- HK36 (motor glider)
- M20T (turbocharged Mooney)
- PA12 (Piper Super Cruiser… on floats!)
- PA28
- PA32
- PA34
- PA38 (with a very slender student!)
- PA44
- PA46 (Malibu; the dream family airplane as long as one can get a letter from God promising that the engine won’t quit)
- PC12
- R22
- R44
- R66
- SGS 2-32 (glider)
- SGS 2-33 (glider)
- SR20
- SR22
- TBM850
Adding to this blog so that the information doesn’t get lost. I was thinking that it would be good to put the favorites in bold, but I realized that at least half of the above aircraft would need to be marked. Most of them have at least some great characteristics.
The list would be a bit longer if I included variants, e.g., the turboprop versions of the PA46, the retractable version of the PA28, or the turbocharged version of the SR22.
Despite FAA English proficiency requirements for certificate holders, I am having some trouble understanding this new copilot. I think that he is complaining about the lack of A/C in the Cirrus:
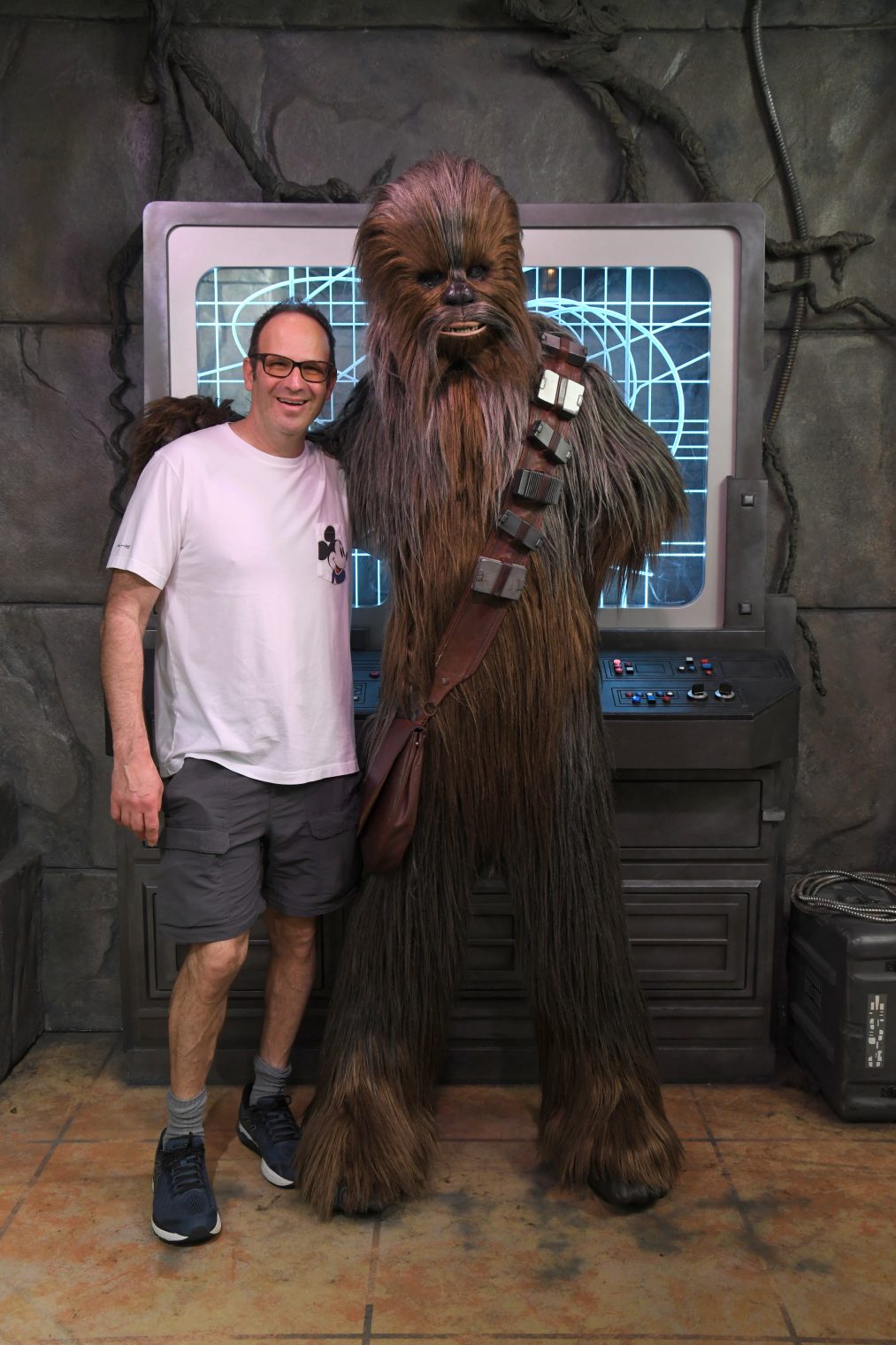